- 日本通運トップ > サービス・ソリューション > 事例集 > 国内ソリューション事例 > グリーンロジスティクス事例 > モーダルシフト事例-2
モーダルシフト事例-2
飲料メーカー様の工場間輸送における改善事例概要
工場間輸送において、鉄道用20ft大型コンテナ、海上用トレーラーシャーシなどの輸送モードを加え、お客様の出荷数量や納期に合わせたモーダルシフトを往復実車で実現することにより、CO2排出量削減を達成した事例です。
改善前の問題点
これまで株式会社E様では、松山工場と東京工場間の工場間輸送を行っていましたが、それぞれ発地側の工場が独自に輸送を手配しており、大型トラックが主な輸送手段となっていました。出荷数量が少ない時は、鉄道用12ftコンテナを利用することもありましたが、更なる運搬具の大型化の為には、専用運搬具導入が必要であり、環境負荷低減を志向しながらも、廻送の問題などが懸念され、モーダルシフトが難しい状況でした。
改善のポイント
鉄道用12ftコンテナを越える出荷数量(ロット)に対応する為、鉄道用20ft大型コンテナ(専用)、海上用トレーラーシャーシ(専用)を導入することによって、出荷数量(ロット)や納期に合わせて、現状の大型トラック以外に複数の輸送手段を選択できる体制を構築しました。また、それぞれ発地側の工場で手配していた輸送を、本社のある松山側に一本化したことにより、専用コンテナや専用シャーシの廻送を考えながら、往復実車輸送する仕組みを構築し、CO2排出量の大幅削減を達成しました。
改善前のフロー
従来のトラック輸送による工場間物流の概要
- 松山工場から東京工場
- 発側工場が独自に輸送手配
- 輸送距離(片道):852km(陸路)
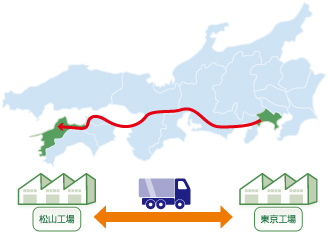
改善後のフロー
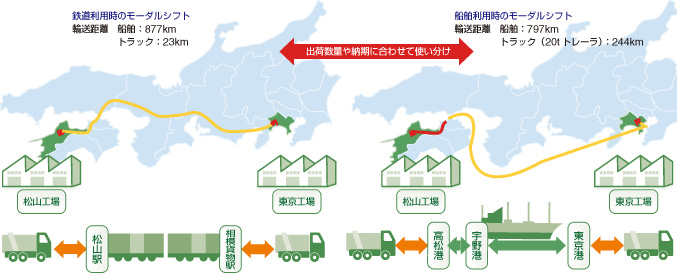
改善効果
鉄道用12ftコンテナ、鉄道用20ft大型コンテナ、海上用トレーラーシャーシを、出荷数量や納期に合わせて使い分け、窓口一元化による往復実車輸送を実現したことで、実施前に比べ50%以上のCO2排出量削減が達成されました。